Belt drying lines for the production of high quality gelatin
Gelatin is pure protein and is colorless or slightly yellow, it is nearly tasteless and odorless. Gelatin is made from fish, pig skins and bovine bones. It is commonly used in food, pharmaceutical, photography and cosmetic manufacturing industry. Gelatin is also known as number E441.
Gelatin has a unique characteristic, it melts when heated up but solidifies again when cooled down. Together with water it forms a semi-solid colloidal gel and sticks enormously.
The production of gelatin helps to make the meat processing industry more sustainable as all waste streams are turned into useful products. Gelatin is produced in a complex, multi-stage process using high-tech industrial equipment. The high quality standards for gelatin are ensured through the choice of raw materials and the production process.
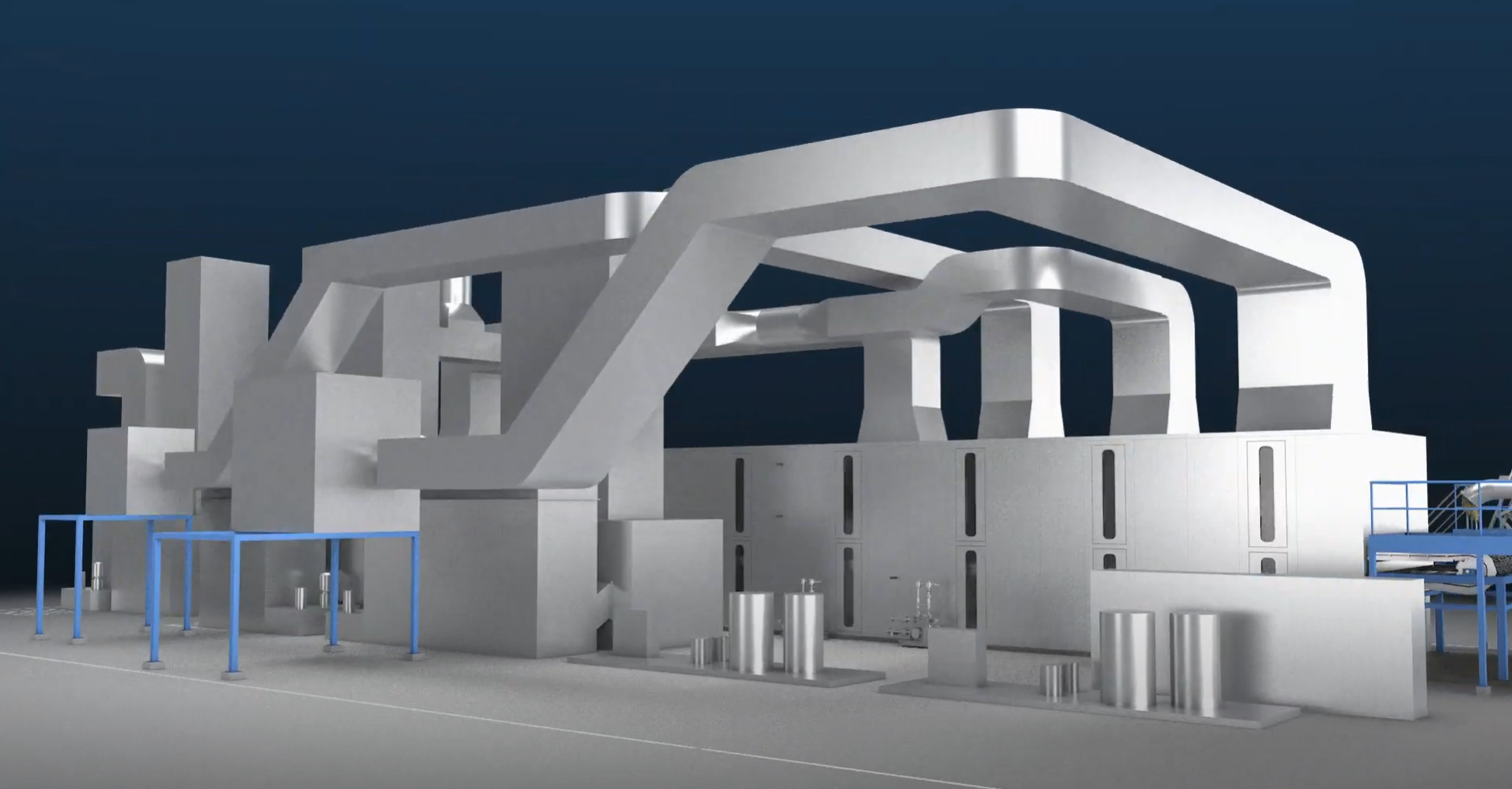
How does a belt and air drying solution for Gelatin industry work?
TEMA Process belt dryers combine a hygienic liquid-desiccant air dehumidifier with a multi-zone, temperature-controlled conveyor to dry gelatin noodles quickly, safely and economically. Ambient air is washed with a hygroscopic salt solution that removes moisture and destroys up to 99 % of airborne bacteria, then directed through successive compartments where temperature is gently ramped to prevent melting. Integrated heat recovery lowers energy use up to 40 %, while custom low-shear fans eliminate hot spots and guarantee uniform moisture removal. A final cooling section and inline mill deliver free-flowing powder ready for downstream processing. The result is consistent bloom value, long shelf life and the lowest cost-per-kilogram gelatin on the market. Trusted worldwide, the Dutch-built system meets strict food and pharma standards today.
The primary applications for raw material gelatin
The primary applications for raw material gelatin
Gelatin is mainly used in the food industry, pharmaceutical products or used as an industrial application.
Examples for the food industries:
Examples for the pharmaceutical industries:
Examples for the industrial application:
Scope of supply for the gelatin industry
- Extruder or votator to transform gelatin from liquid to solid state
- Chiller with buffer tank and pump for the votator
- Belt dryer to dry gelatin to 10 to 12% moisture content
- Milling and grinding dry gelatin
- Metal detection systems for dry gelatin
- Dehumidifier for supplying cold, dry and bacteria free air to the belt dryer
- Hot water system to maximize the belt dryer output
- Heat pump system to minimize the total energy consumption
- PLC control and automation systems including visualization or SCADA systems
The gelatin extruder or votator is especially designed for cooling and gelling of the gelatin concentrate. Inside the stainless steel tube (a scraped surface heat exchanger), the gelatin transforms from a pumpable liquid into a solid gel. This gel is extruded through a perforated plate in the form of noodles. These noodles will be evenly divided by the oscillating movement of the total votator system. As a coolant glycol at low temperatures is required in order to control the exact temperature of the noodles.
The noodles are deposited on a perforated plate belt dryer in the noodle receiving zone. It’s very important that the noodles are evenly spread on the total width of the belt. The TEMA gelatin belt dryer is a particularly gentle thermal treatment, it can dry large quantities of gelatin with high initial moisture contents. As gelatin is very temperature sensitive the drying process should be controlled (temperature and humidity) continuously and requires a long residence time.
The gelatin dryer is divided into segments (drying zones) in order to create high air velocities with a lower air volume. Fans and heaters are placed inline on the floor and will heat up the saturated and cooled air again. This allows the use of low temperature heating media (preferably hot water) and a smaller total airflow which is repeatedly heated up.
Hygienic Design for Bacteria-Sensitive Gelatin Processing
As gelatin is very bacteria sensitive the belt dryer is designed as hygienic as possible. Perforated plate segments can be cleaned using water. The dirty water can be drained through a gutter which will be integrated in the concrete floor of the dryer.
The air used for the gelatin drying process needs to be filtered, cleaned and dehumidified first, our liquid desiccant dehumidifier is a perfect solution for these process steps (see dehumidification with a salt solution). Dehumidified air passes the gelatin layer in a downstream and upstream flow in order to dry the gelatin with a maximum uniformity.
By continuously controlling the airflow, temperature and humidity during the gelatin drying process the product output capacity will be maximized and the energy consumption will be minimized.
Milling and Grinding dry gelatin
At the end of the belt dryer the dry gelatin will be grinded into large pieces. The rough grinder is integrated in the drive frame of the gelatin dryer. These pieces of 10 to 20 mm. are transported to one side of the belt dryer using a vibrating chute.
With an additional fine grinder, the coarse gelatin is milled dust-free and in free-flowing qualities. Grinding process fineness values are common between the 8 and 40 µm. After milling the dry gelatin powder is distributed to the blending department using a pneumatic transport system.
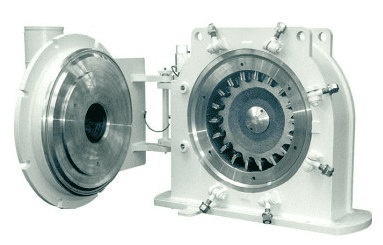
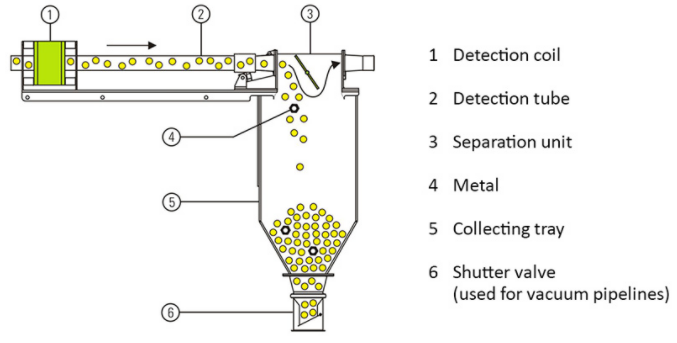
Metal detection
Our gelatin drying lines can be implemented with a free fall metal detection system. This free-fall metal detection systems benefit from a very high sensitivity for the detection of all types of metal. Our powder metal detectors are designed with a range of high-speed reject mechanisms to remove metal-contaminated products from the manufacturing process.
Dehumidifying with a salt solution
The Tema Process air dehumidifiers have been developed for cooling, dehumidification and microbiological decontamination of industrial process air. These reliable systems ensure a constant humidity and constant air temperature throughout the year, regardless of outside air conditions or fluctuations in the indoor climate. Dehumidification as low as 15% relative humidity can be reached at low temperatures (-20 to +40°C).
The Tema Process dehumidifier is using a Lithium Chloride salt solution as absorbent. Lithium Chloride is a very strong salt and has an equilibrium curve which closely follows the relative humidity curve of air. The process air will enter the countercurrent dehumidifier and will be dehumidified or humidified in order to maintain this equilibrium. In other words the sprayed salt concentration will control the outlet air relative humidity. By cooling the salt solution before spraying we are able to cool down the air temperature. In this way air temperature and air humidity are both controlled in the same system but can be adjusted independently.
As moisture is continuously absorbed by the salt solution inside the dehumidifier, it becomes diluted and slowly loses drying capacity. To evaporate this surplus of moisture the absorbent is pumped to the regenerator unit. Here the process is turned around, so by heating up the salt solution, moisture is released to an outside air stream and exhausted. The salt solution is continuously pumped between the units in order to provide precise conditions to the process.
Lithium Chloride is a chemically stable, non-toxic, non-vaporizing salt solution which acts as a biocide to mold, bacteria and micro-organisms. Beyond its physical desiccant nature Lithium Chloride is also an effective antifreeze.
Advantages of a belt dryer in the gelatin industry
Advantages of a belt dryer in the gelatin industry
Interested?
Exploring options for your process? TEMA Process is here to assist. Whether you have specific questions or need guidance in selecting the right solution, our experts are just a call or email away. Leave your contact details, and one of our specialized team members will promptly get in touch. They’ll provide you with all the necessary information about our advanced solutions, tailored to meet your unique requirements. Let TEMA Process be your partner in achieving optimal product quality and safety
Hot water system
One of the key advantages of the TEMA belt dryer is the possibility to run on a hot water system instead of steam. As our belt dryer is using multiple drying zones which are all equipped with their own heating coil it’s easy to reheat the cooled down and saturated air again. The approach temperature between water and the desired air temperature is designed as small as possible. This kind of heating will result in a more accurate temperature control and helps achieving a uniform air temperature inside the whole drying zone.
Big advantage of such an accurate air control system is that you prevent wet gelatin spots. These spots can occur when certain areas are drying slower because of a lower air temperature for example. It can also create case hardening when the gelatin dries too fast and air temperatures are too high. This means the outside layer is already completely dried out but inside the gelatin is still wet. The outside layer will form a shell and water is not able to migrate to the outside anymore.
Extra benefit because of using this lower temperatures is less heat loss and therefore an energetically better system. To optimize the temperature control even more we can install a water injection system on every heating coil. By doing this we create a constant waterflow over the coils and vary the water temperature.
To heat up the hot water system multiple installations can be used: steam, gas fired or thermal oil if available. From an energy point of view it’s very interesting to use an electrical heat pump system.
The additional “free” chilled water from the heat pump can be used for the dehumidifier.
Sensors, control panel and visualization
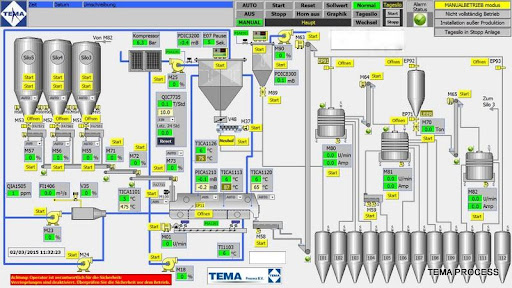
The Tema Process control panel will steer, manage, calculate, control, monitor and protect the complete solution. These can be mechanical, hydraulic, electrical and/or pneumatic sensors, dampers and valves. They are all connected to the PLC control system, which can be easily integrated into the complete industrial automation system of your factory.
We have the experience with
- Programming of different PLC brands (mostly Siemens or Rockwell, Allen Bradley)
- Visualization of production processes by means of HMI and/or SCADA
- Remote control and can be linked to building management systems
Commitment to Sustainability
At TEMA Process, sustainability is at the core of our operations.Our innovative drying and processing solutions are meticulously engineered to reduce environmental impact, while enhancing efficiency and productivity. By transforming residual products and waste into valuable resources we support the circular economy and contribute to a greener future.
Gelatin related Articles
Want more info? download our technical sheet
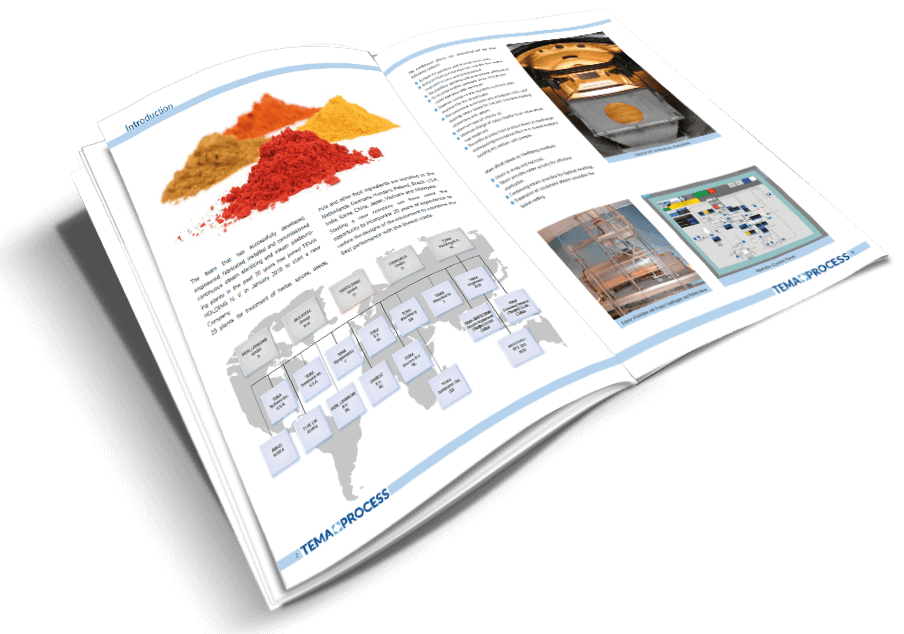
Gain a comprehensive understanding of our diverse product range through our detailed technical sheets. Available in multiple languages, these sheets offer key insights to inform your decisions.
Enhance your knowledge with images included in our sheets that help elucidate the processes and their applications, making it easier for you to visualize and grasp the practical aspects of our products.