At TEMA Process, we understand the critical importance of maintaining air quality in industrial settings. Our dust collection systems are engineered to capture a wide range of dust particles, from fine to coarse, enhancing the overall efficiency of your operations. Whether you’re dealing with the challenges of processing minerals, chemicals, food, feed, or biomass, our dust collection solutions are tailored to meet your specific requirements.
Our commitment to innovation and quality ensures that our dust collection systems not only meet but exceed industry standards. With TEMA Process, you can expect robust design, efficient operation, and minimal maintenance requirements, all contributing to a more sustainable and environmentally friendly production process.
TEMA Process B.V. offers Dust Collection & Gas Scrubbing equipment and systems for emission control, gas cleaning and product recovery. TEMA Process designs the Dust Collection & Gas Scrubbing equipment and systems in accordance to the latest standards, local conditions and product specifications.
Tema Process Dust Collection & Gas Scrubbing Line include: Jet bag Filters, Cyclones, Venturi Scrubbers, Packed Tower Scrubbers, Dry Scrubbers, Cyclones in combination with Jet bag Filters, Cyclones in combination with Packed Tower Scrubbers
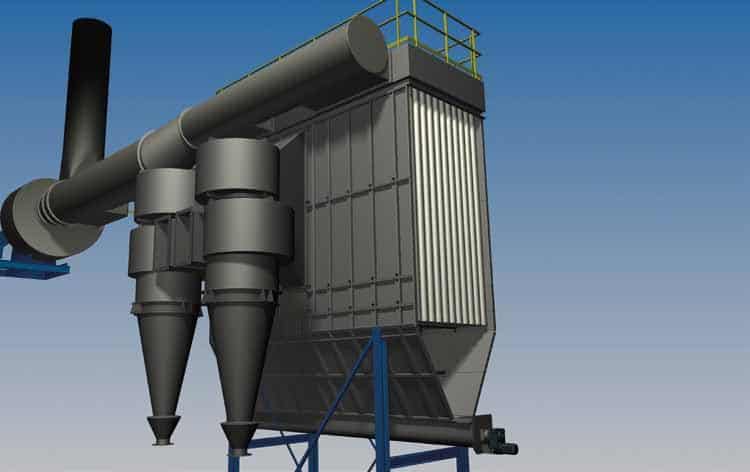
Understanding Cyclones in Dust Collection
Cyclones are a critical component in the field of industrial dust collection, offering a cost-effective solution for the removal of particulates from air streams. Utilized across various industries, cyclones operate on the principle of centrifugal separation, ensuring a cleaner and safer working environment.
Working Principle
Centrifugal Force for Particle Separation: Cyclones use centrifugal force to separate dust and particulate matter from industrial exhaust gases. The air containing dust enters the cyclone at a high velocity, typically tangentially. This rapid entry creates a spiral motion, forcing particles to the cyclone\’s walls. Due to gravity, these particles then descend into a collection hopper.
Advantages of Cyclone Systems
Efficiency and Cost-Effectiveness: Cyclones are highly efficient for large particle separation and are cost-effective, requiring low maintenance. They can handle high temperatures and pressures, making them suitable for a wide range of industrial applications.
Versatility and Durability: Their robust design allows them to withstand harsh industrial environments. Cyclones can be used as standalone units or integrated with other dust collection systems for enhanced performance.
Applications in Various Industries
Broad Industry Utilization: Cyclones are used in woodworking, metalworking, food processing, pharmaceuticals, and more. They are essential in industries where large amounts of dust and debris are generated, ensuring compliance with environmental and health regulations.
Environmental Impact and Safety
Reducing Environmental Footprint: By efficiently removing particulates from emissions, cyclones contribute to a reduction in environmental pollution. They also play a crucial role in maintaining air quality standards in industrial settings.
Enhancing Workplace Safety: Cyclones minimize the risk of dust-related hazards, including respiratory issues and potential explosions, thereby ensuring a safer workplace.
Conclusion
Cyclones, with their efficient particle separation, versatility, and durability, are an indispensable tool in industrial dust collection. By implementing cyclone technology, industries not only enhance operational efficiency but also contribute to environmental conservation and workplace safety.
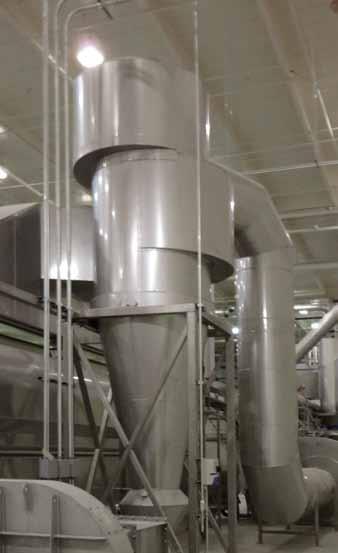
A Cyclone is a relative simple device that uses centrifugal force to separate larger particles from air streams.
It is a high capacity / high efficiency separator that also can be used in combination with fluid bed Dryers / Coolers, Jet bag Filters, Packed Tower Scrubbers and other process equipment. Diameters from 400 to 2000 mm.
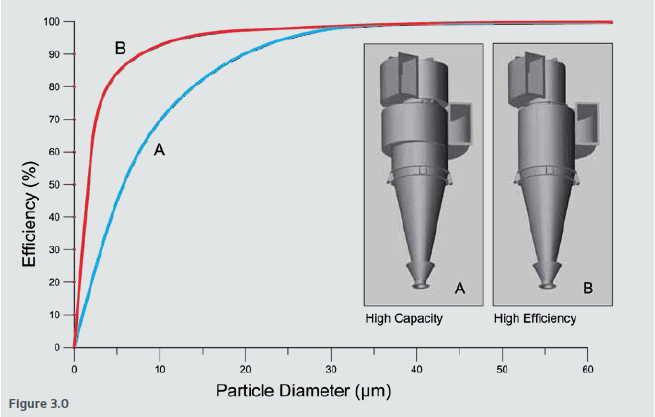
Jet Bag Filters
TEMA Process design for continuous Jet bag Filters is based on the process data and local conditions and can be offered “Taylor-made” suitable for the application
Important criteria for the design are:
- Gas volume in Nm³/
h
- Chemical composition of the gases
- Moisture content of the gases
- Temperature of the gases
- Dust in kg/h
- Characteristics of the dust, like corrosive, abrasive etc.
- Particle size range of the dust
- Local emission standards
- Explosion resistant (ATEX)
- Hygienic design
- On line or off line systems
- Materials of construction
The filter top part can be designed based on following variables:
- Number of covers
- Layout of the covers
- The covers can be located on one side or 2 sides of the air buffer tanks
- Under each cover there are 4 rows in width and 8 – 16 filter bags in depth
- Materials of construction can be selected in accordance to the table of “construction materials”
- The top part is standard made of stainless steel and is isolated.
- The top part can be provided with double covers.
- The bags are protected by standard wear protection shields
- The maximum number of covers on one side of the buffer tanks are 4 (maximum 4 covers on each side!)
Length of filter bags are available from 2000 mm – 5000 mm
- Bag support cages can be split in length in several parts for one filter bag with easy connection to reduce space for replacement of the filter material
- The textile bags can be supplied in different qualities
- The filter housing is designed in several “modules”
- The dust is collected in a tapered chute with an integrated spiral screw for dust discharge
- The location of the screw discharge also can be chosen to meet local dust collection or transport
- The 3D design drawing is the base for laser cutting- and production drawings
- An enormous number of construction variations are possible considering the variables in number of covers, number of bags in the length rows and filter bags length
Venturi Scrubber
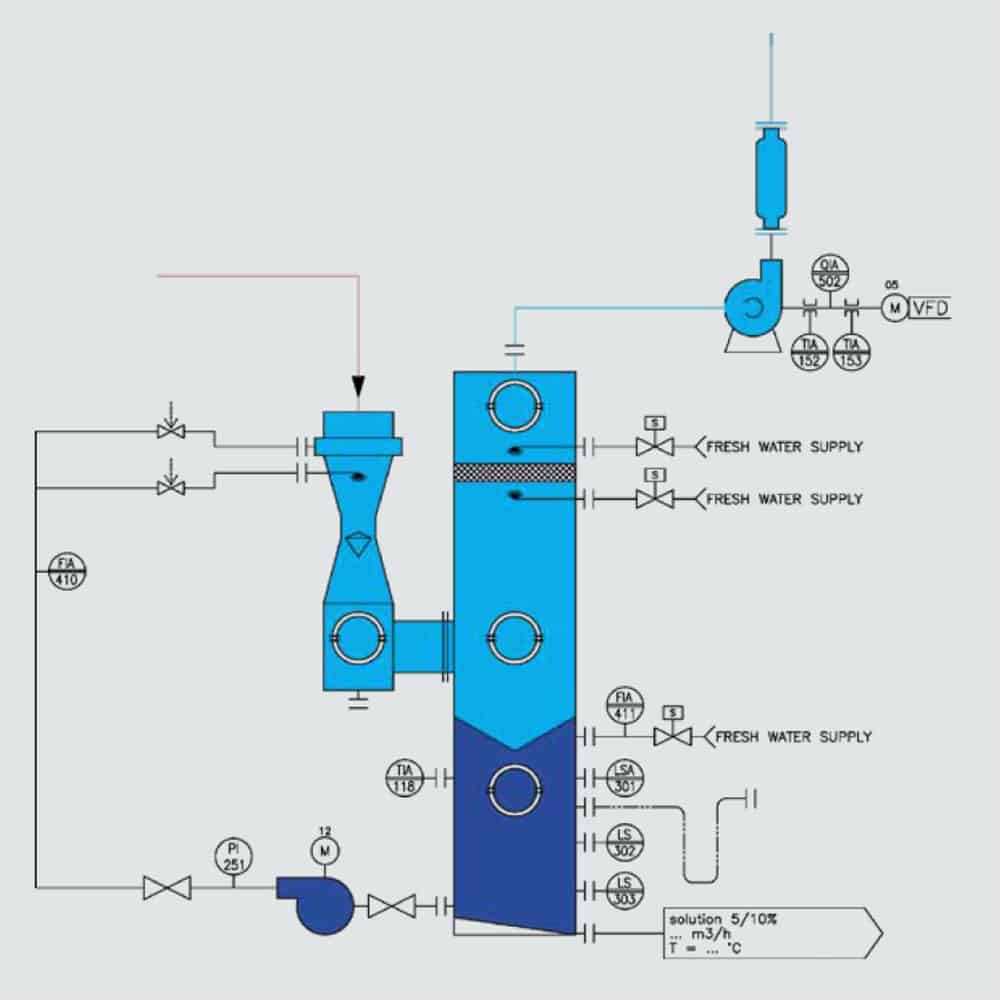
Venturi scrubbers are used to remove particulate matter from a gas stream. A „Venturi Scrubber“ consist of a contact section called a venturi section in combination with a droplet separator section.
Exhaust gas with dust is fed into the venturi section where it passes through a water mist at the venturi throat at high velocity. This results in thorough mixing of water droplets and dust particles which agglomerate to form larger particles which are subsequently removed from the gas in the separator section.
The water supply units and spraying systems allow recirculation of water with high dust contents. These systems are used for cleaning particulate matter from exhaust gas with stringent emission level, soluble dust mainly in the mineral and chemical industry.
Packed Tower Scrubber
Packed tower scrubbers are used to remove particulate and / or vapor contaminants from an exhaust gas stream by way of dilution or absorption.
A packed tower is an efficient method of carrying out mass transfer between gas and liquid phases. Packed tower scrubbers incorporate packing media
to facilitate intimate contact between a scrubbing liquid and gas to be scrubbed.
Applications are: reduction of dust or gaseous emission levels, product recovery, air pollution and odor control.
In countercurrent scrubber operation, the gas flows upward through the packing material, while the liquid flows downward by gravity through the
packing material. The liquid wets the surfaces of the packing material, providing a large amount of surface area for diffusion of one or more components of the gas stream into the liquid stream, thereby cleaning the gas.
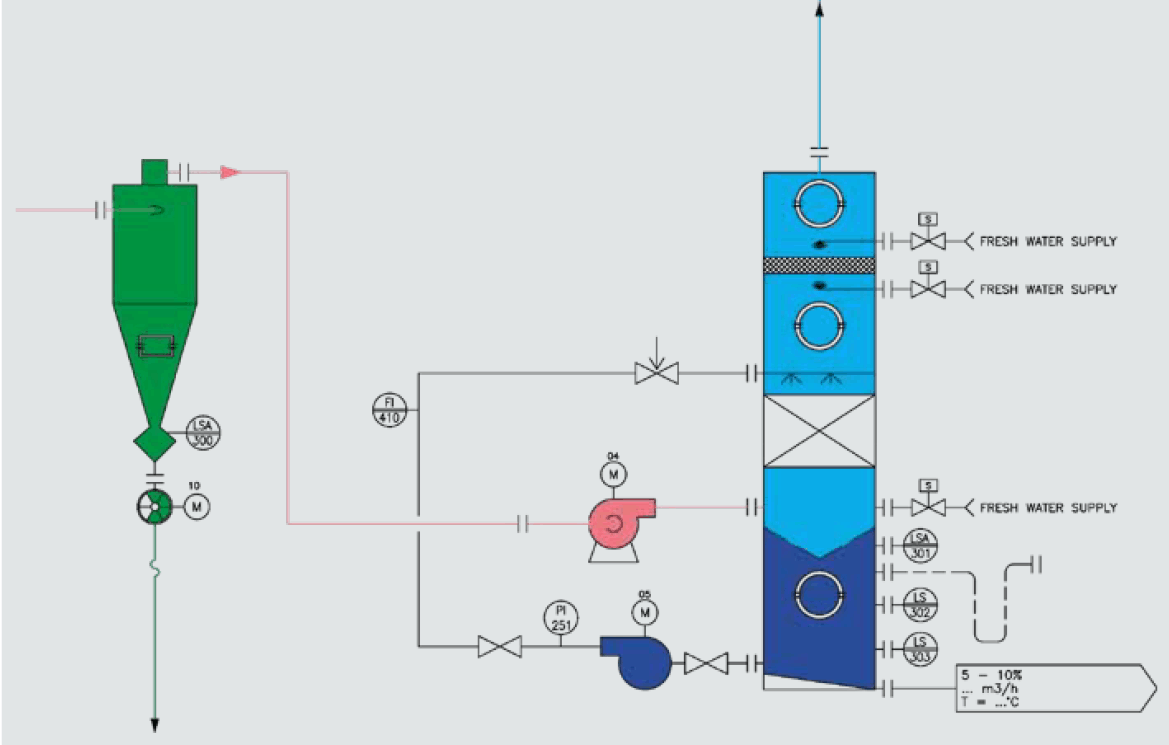
Commitment to Sustainability
At TEMA Process, sustainability is at the core of our operations.Our innovative drying and processing solutions are meticulously engineered to reduce environmental impact, while enhancing efficiency and productivity. By transforming residual products and waste into valuable resources we support the circular economy and contribute to a greener future.
Interested?
Exploring options for your process? TEMA Process is here to assist. Whether you have specific questions or need guidance in selecting the right solution, our experts are just a call or email away. Leave your contact details, and one of our specialized team members will promptly get in touch. They’ll provide you with all the necessary information about our advanced solutions, tailored to meet your unique requirements. Let TEMA Process be your partner in achieving optimal product quality and safety