Continuous fluid bed dryer
TEMA Process offers a range of continuous fluid bed dryers and coolers, designed to accommodate various types of materials and industrial requirements. The continuous process can be implemented in both static and dynamic (shaking vibrating) fluid beds.
In a static fluid bed, uniform materials that do not tend to agglomerate are processed. One of the unique features of these units is the option to include submerged heat exchangers. This allows for energy input from both the fluidizing air and the heat exchangers, thereby optimizing the energy efficiency of the process. The integration of submerged heat exchangers not only enhances the energy efficiency but also reduces the size of the equipment and limits the volume of exhaust air.
On the other hand, dynamic (shaking vibrating) fluid bed units are designed for continuous operation and are particularly suitable for materials that are sticky and have a wide particle size distribution. The shaking motion in these units significantly enhances the fluidization and transport of materials within the bed. This ensures an even and efficient drying process. The dynamic fluid beds can achieve drying gas temperatures up to 750 °C and product temperatures up to 400 °C, making them suitable for a wide range of industrial applications.
These continuous fluidized bed dryers and coolers are a testament to TEMA Process B.V.’s expertise in thermal and physical process equipment manufacturing. They demonstrate the company’s ability to offer customized solutions that cater to the diverse needs of various industries, ensuring high efficiency and quality in their processes. The continuous fluid bed dryer technology is a key component in this, offering precise control over drying and cooling conditions, leading to optimal product quality and energy efficiency.
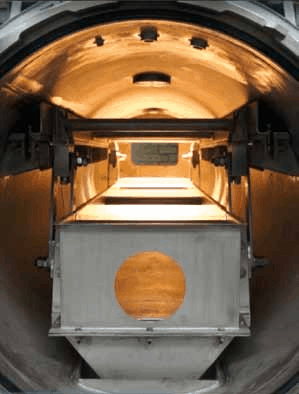
How does a continuous fluid bed dryer work?
A fluid bed dryer can handle up to 200 t/h and is used for drying of clay, sand, gravel, limestone, etc.
A continuous fluid-bed dryer/cooler is a machine in which a continuous flow of damp, granular material is conveyed over a perforated bed, through which air is blown to bring about fluidization. The material is dried in the first section of the machine and cooled in the second. Drying occurs because of the direct contact between the damp material and the hot air blown through it. The air velocity is adjusted to keep the moving layer of material fluidized. The same mechanism applies to the cooling part of the process, except that the air used is either ambient or conditioned (ie cooled). The drying and cooling sections of the machine form a single conveyor in which the hot and cool air flows are segregated. Conveying of the product is achieved either by means of a low-frequency, high amplitude shaker mechanism.
Fluid bed dryers are specially preferred in mineral drying in combination with after cooling and heat recovery, resulting in better end product quality and very low energy consumptions.
Advantages of continuous fluid-bed dryer system technology
Advantages of continuous fluid-bed dryer system technology
Fluid bed dryers & coolers
How does a fluid bed dryer work?
A continuous fluid-bed system is a machine in which a continuous flow of “wet” powder, granular or flakes material is conveyed over a perforated bed. Hot drying air is blown through the holes of a perforated plate. The wet solids are lifted from the bottom and causes the solids to behave as a fluid. The air velocity is adjusted to keep the moving layer of material fluidized.
Conveying of the product is achieved by means of a low-frequency, high amplitude shaker mechanism. The “Shaking” motion plug flow of the Tema fluid bed, allows first-in, first-out drying of products and well-mixed fluidization, which covers the entire spectrum and is able to accurately control the spread of residence time.
Types of Fluid bed dryers
Fluid bed units
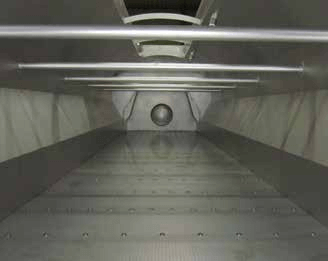
A fluid bed is an effective unit to thermally treat powders, crystalline products, pelletized or extruded materials. High heat and mass transfer are obtained as a result of the intimate contact between fluidizing air and product.
Shaking fluid bed
units for continuous operation and suitable for sticky materials with a wide particle size distribution. The shaking motion improves the fluidization and transport of any material within the fluid bed. Drying gas temperature up to 750 °C and product temperatures up to 400 °C are achieved
Static fluid bed
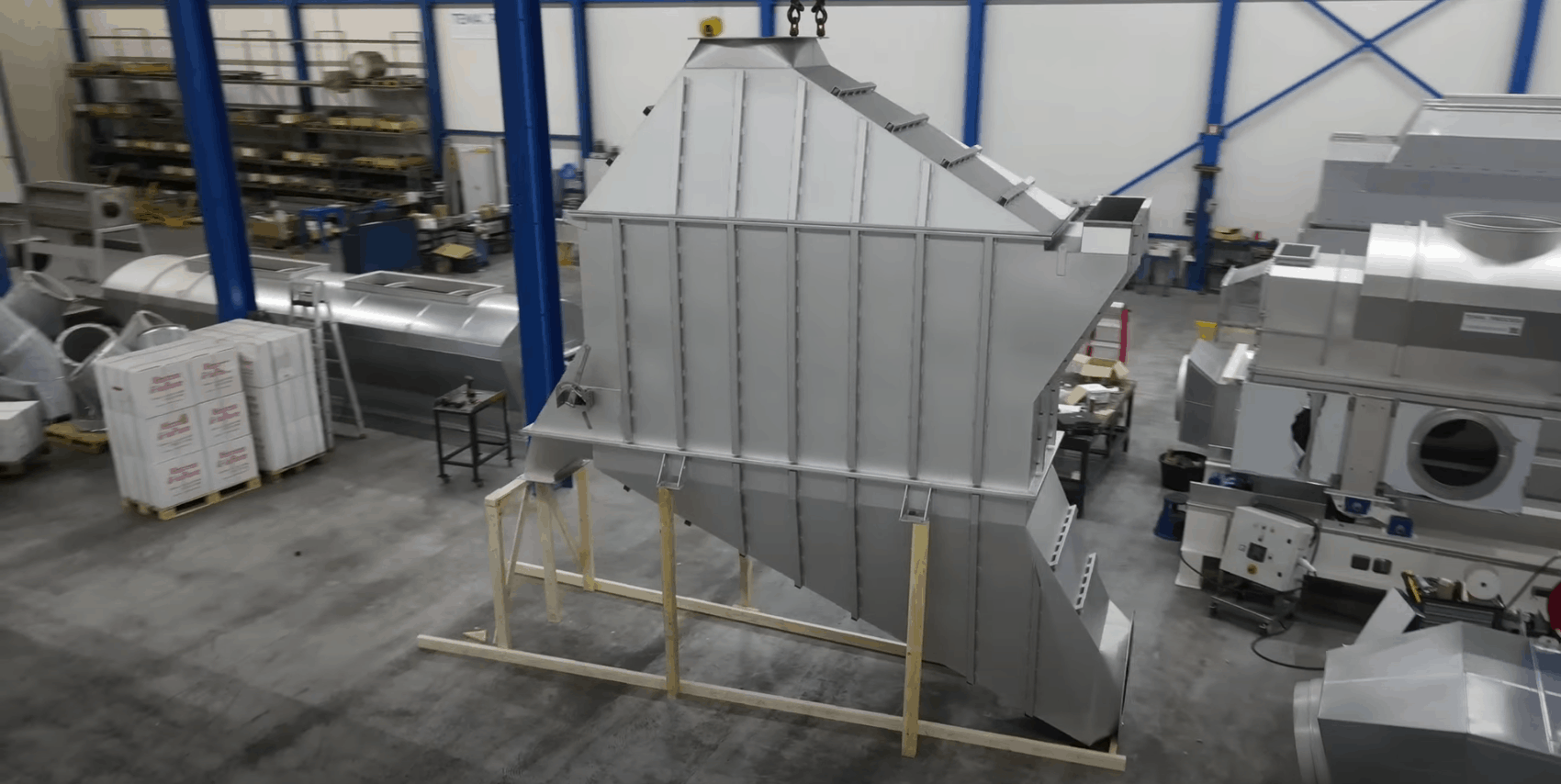
units in continuous and batch type for more uniform materials that do not tend to agglomerate. It is possible to install submerged heat exchangers in a deep static bed. With submerged heat exchangers energy input is both from the fluidizing air as well as from the heat exchangers reducing the size of the equipment and limiting the exhaust air volume.
Interested?
Exploring options for your process? TEMA Process is here to assist. Whether you have specific questions or need guidance in selecting the right solution, our experts are just a call or email away. Leave your contact details, and one of our specialized team members will promptly get in touch. They’ll provide you with all the necessary information about our advanced solutions, tailored to meet your unique requirements. Let TEMA Process be your partner in achieving optimal product quality and safety
TEMA Process: Custom Fluid Bed Dryer Manufacturing

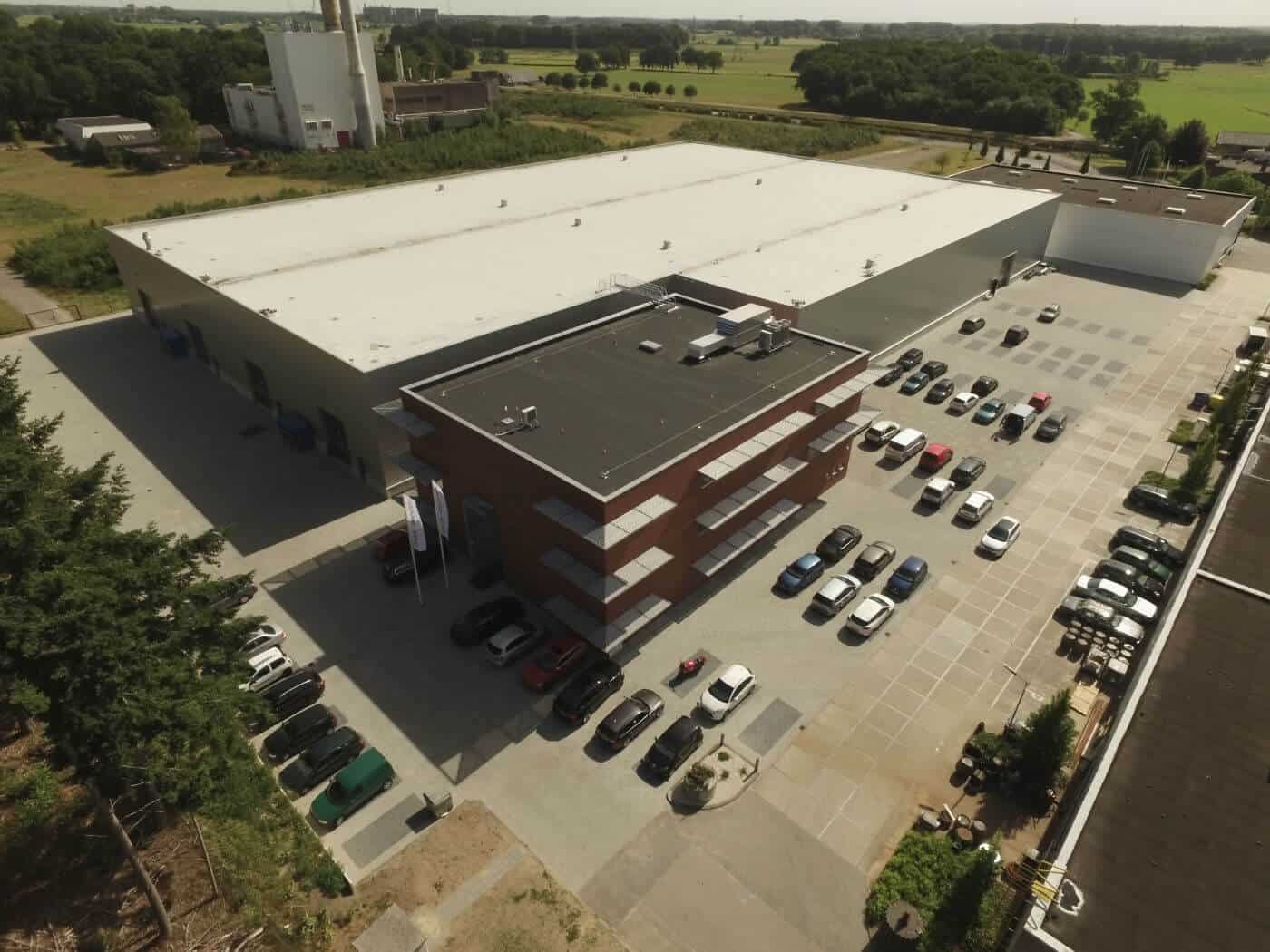
To prepare for further growth, TEMA Process BV in has moved to its new engineering ( 1800 m2) and production ( 8000 m2) facility in the Netherlands. The new facility was built under management of TEMA Process BV and is totally fit for manufacturing of fluid bed dryers, coolers and associated equipment.
Expertise in Fluidized Bed Dryer Design and Engineering
TEMA Process specializes in the design, engineering, testing, and installation of custom fluid bed dryers for a variety of industrial applications. As a leading fluid bed dryer manufacturer, we focus on delivering high-quality, custom-made drying solutions tailored to the specific needs of your factory.
Precision Engineering for Optimal Performance
Our fluidized bed dryers are engineered with precision, ensuring that each machine meets the specific requirements of your production process. Our team of experienced engineers collaborates closely with you to develop dryers that integrate seamlessly into your existing systems, enhancing efficiency and productivity.
Comprehensive Testing and Installation
Every fluid bed dryer from TEMA Process undergoes rigorous testing to guarantee performance and durability. Our commitment to quality extends from the design stage through to the final installation in your facility, ensuring that our machines operate optimally within your production environment.
Reliable Solutions for Your Drying Needs
As your fluid bed dryer manufacturer, TEMA Process is dedicated to providing solutions that enhance the productivity and efficiency of your operations. Our custom-engineered fluidized bed dryers are designed to meet the unique challenges of your factory, delivering reliable and effective drying performance.
Want more info? download our technical sheet
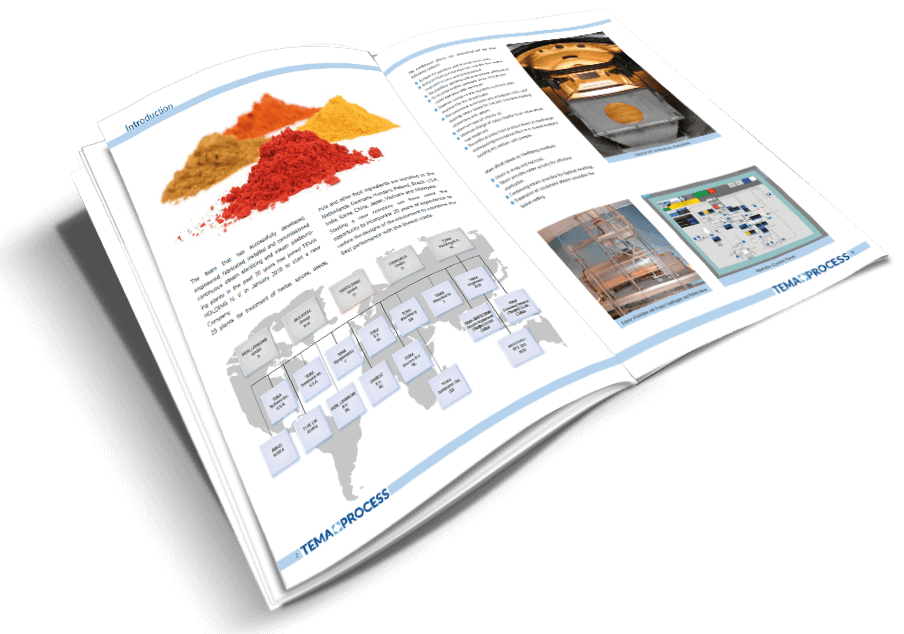
Gain a comprehensive understanding of our diverse product range through our detailed technical sheets. Available in multiple languages, these sheets offer key insights to inform your decisions.
Enhance your knowledge with images included in our sheets that help elucidate the processes and their applications, making it easier for you to visualize and grasp the practical aspects of our products.